Water management at Fresenius Kabi
Periods of drought, flooding, and diseases caused by contaminated water – water risks are one of the most urgent global challenges. As a healthcare company operating across the world, we want to be part of the solution. Water management promoting conservation of resources is therefore a top priority for us.
Every drop is valuable: The facts around our approach to water
Our objective is to use the vitally important resource of water responsibly. This is why we closely monitor the quantities we consume through our business activities. The absolute volume of water that we withdrew and used in the course of our business activities during 2023 amounted to 9.9 million m3.
Where does 9.9 million m3 of water flow to?
Water usage and withdrawal
In the areas of clinical nutrition, intravenously administered drugs, infusions, and biopharmaceuticals, it is vital for patients that the purity of the products is guaranteed and the cold chain is maintained. Some of the water we use is to produce steam for sterilization, and water-based cooling and cleaning processes. However, sterile water is highly purified and it is an essential component in the manufacture of medical products, and medicines. Sterile water used for purposes like infusion and rinsing solutions such as sodium chloride must meet stringent quality requirements to ensure product quality and patient safety.
How we identify water risks and deal with them
Like most manufacturing companies, Fresenius Kabi is dependent on water as a raw material in its production processes. But clean water is in increasingly short supply throughout the world.
We therefore make it a priority to precisely assess the water risks present at our various production sites. Fresenius-Kabi uses the Aqueduct Water Risk Atlas of the World Resources Institute (WRI) to analyze the availability of water at specific locations.
Aqueduct Water Risk Atlas of the World Resources Institute (WRI)
In collaboration with companies, governments, and research partners, the institute set out to drive forward proven procedures for managing water resources, and facilitating sustainable growth in a world beset by water shortages.
The tool allows us to access publicly available peer-reviewed data to map water risks such as floods, droughts and water stress1. This gives us information about the current and future water risks at our locations.
All our production sites carry out a climate risk assessment. This includes water risks like flooding, droughts, and heavy rainfall, and the sites must take appropriate measures if a risk is identified.
Our measures for reduction of water consumption
A number of different approaches have been adopted to reduce our water consumption. At some production sites, we use water a number of times, e.g. through the use of steam condensate recovery systems at our sites.
In 2023, we launched several projects at the production sites directed toward saving water. One example is the objective of using water more sustainably in wastewater treatment systems and recycling programs. In addition, we optimized the cleaning and sterilization processes at several sites.
Our approach to reducing water consumption at our sites
Beijing, China: Water recycling during coating
The coating of tablets is common practice for pharmaceuticals, for example to control the time and amount for the release of active ingredients. This process also uses solvents that release organic gases. These gases have to be absorbed by spray water in scrubbers. At our production site in Beijing, around 35% of the water consumption is for operation of these scrubbers. In order to reduce our water consumption, we have introduced an innovative recycling process. After water has been used repeatedly, quartz sand and activated carbon are used to filter and disinfect this water so that we can feed it back to the scrubbers. This means that we save an estimated 14,000 m3 each year at our Chinese location.
At the production site we have also adjusted the frequency of changing the pure water required for steam sterilization. By replacing the water every two days (previously once a day), we have been able to reduce annual consumption from 225 m3 to 147 m3.
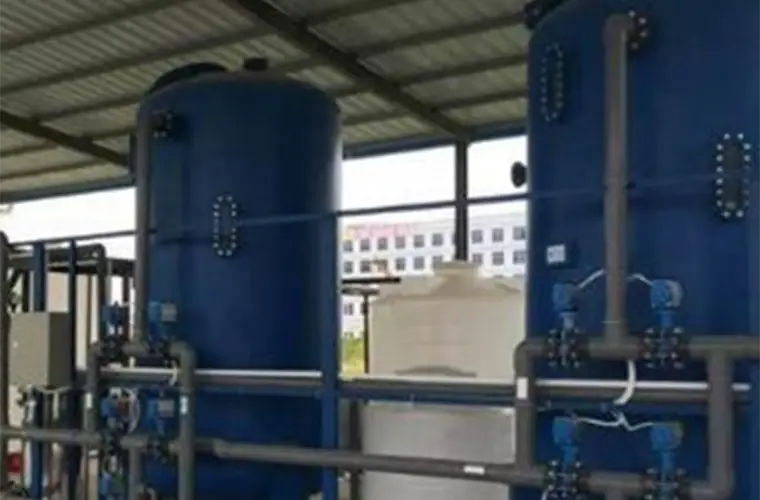
Friedberg, Hessen: Treatment of demineralized water
Conventional minerals (salts) are removed from fully demineralized water (DI water). This is an important resource for the production of pharmaceutical substances. Reverse osmosis systems are used at our production facility in Friedberg to produce demineralized water from municipal water. A concentrate results from the process that consists of water with an increased salt content (10 m3/h). An additional reverse osmosis system enables us to reprocess 40% of the concentrate using a new purification stage, and return it to the input stage of the water treatment system. The returned water has a higher quality than the municipal water. As a result, we are able to cut our consumption by more than 35,000 m3 of water a year and reduce our wastewater volume.
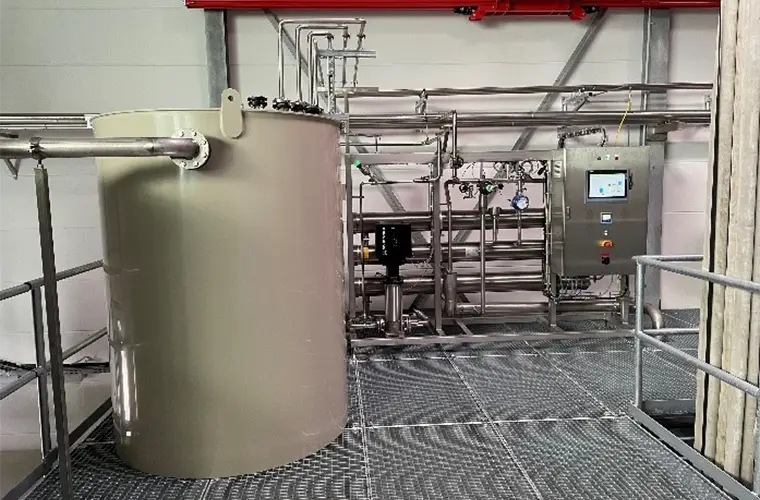
Zapopan, Mexico: Water savings with a purification procedure
At our Zapopan site, we replaced the static spray balls used to clean solvent containers with dynamic nozzles. The design and mode of operation of the newly launched model enable us to clean the interior tank surface more efficiently. This empowers us to reduce the rinsing water by half for each cleaning cycle and save 300 liters of water with each process.
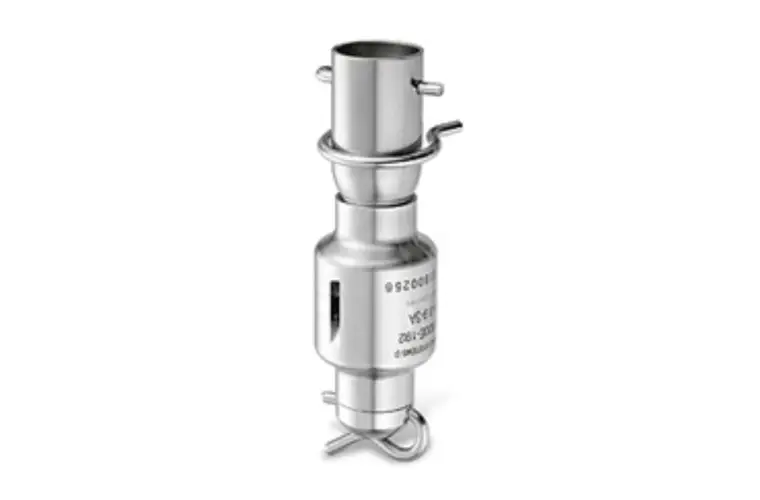
Keeping the water clean: Our wastewater management
Wastewater from industrial production processes can impact the water quality of rivers and springs. In order to prevent this and not put the water quality at risk, we discharge water decentrally at the locations in accordance with applicable local regulations. Production units regularly report wastewater volumes within production to the responsible EHS (Environmental, Health, and Safety) department in accordance with internal standards and guidelines.
Risk of antibiotic resistances – Measures to preserve water quality
Antibiotics belong in people, not in the environment. Nevertheless, drugs can enter the environment through wastewater discharges, and cause antibiotic-resistant bacteria to develop. The consequences can be fatal, if medical treatments lose their efficacy as a result.
To counter this risk, we have been a member of the Antimicrobial Resistance (AMR) Industry Alliance (AMRIA) since 2020, and we have been playing an active role in the management bodies of the alliance since 2021. Furthermore, we have been working on the introduction of the Common Antibiotic Manufacturing Framework (CAMF) of AMRIA. You can find more on this in the Fresenius online Annual Report 2023 in the section water management.
In 2022, AMRIA and BSI Standards Limited released the Antibiotic Manufacturing Standard, providing guidance to the manufacturers on responsible antibiotic production.
The standard complements the environmental and safety management at our production sites. A pivotal component of the approach involves the use of a risk-based methodology to evaluate and control the aquatic waste and water streams generated during antibiotic production – and communication about this at the corporate level.
The mass balance approach
We began implementation of the Antibiotic Manufacturing Standard already in 2022. The focus was on introducing a methodology for the quantification of the mass balance. The template is intended to assist antibiotic manufacturing sites in determining antibiotic concentrations in wastewater discharge from production and in conducting gap analyses. Furthermore, we established a dedicated communication channel to connect local sites together and with the global EHS team. This initiative fosters continuous exchange between the production sites and the global EHS Team to promote the introduction and compliance with the Antibiotic Manufacturing Standard requirements.
1 Currently we are assessing water stress.